How Damon’s HyperDrive is Changing Everything we know about Motorcycle Design
Damon HyperDrive™ is a groundbreaking powertrain and chassis system that integrates all critical components into one unit. It represents a revolutionary leap in electric motorcycle design. HyperDrive uses a monocoque chassis, which means the frame and body are combined into a single, cohesive structure.
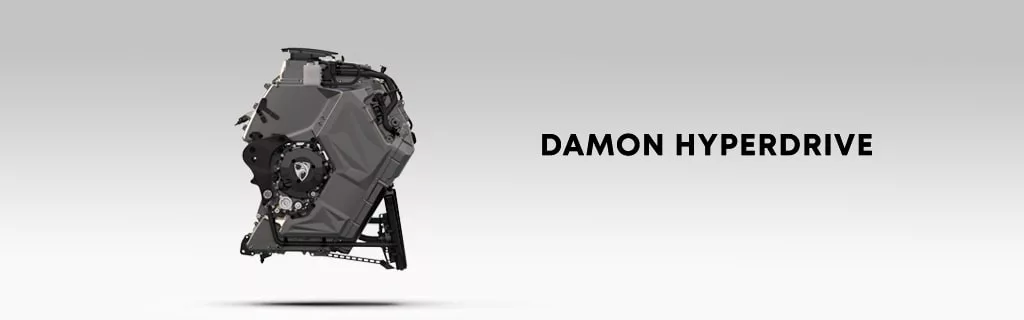
This innovation offers many benefits for electric motorcycles. To truly understand its impact, let’s explore its history, application, and specific advantages.
Why the Monocoque Chassis is Perfect for Electric Motorcycles
To start, let’s examine why the monocoque chassis is an ideal solution for electric motorcycles. The monocoque chassis offers a unique way to simplify and improve motorcycle design. Instead of using a complex aluminum frame, this design combines everything into a single structure that holds all the key components.
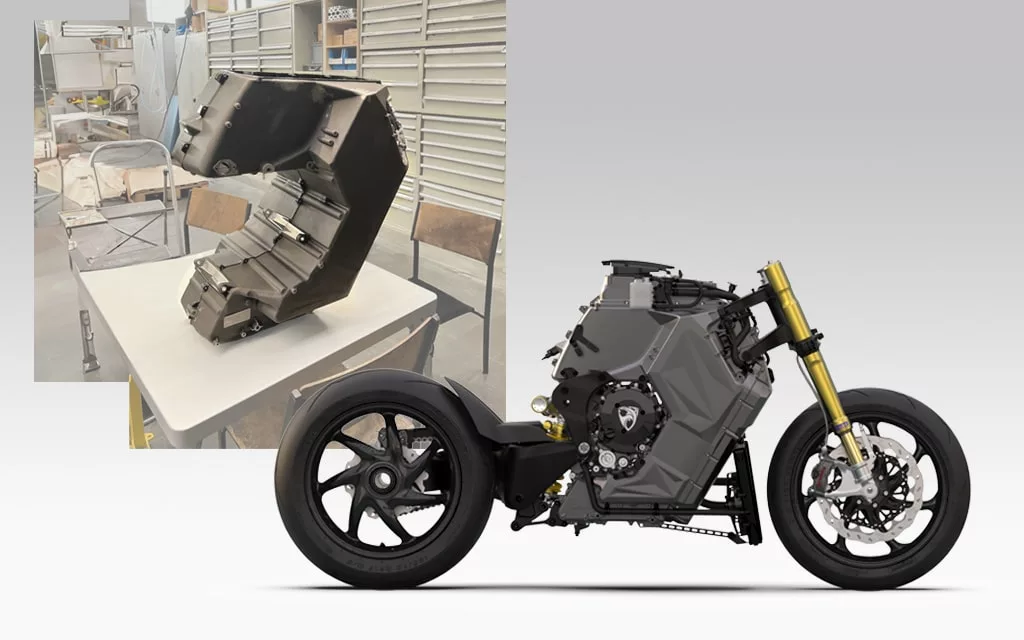
Here’s why this approach works so well for electric motorcycles:
- Mass Reduction: By merging the chassis and electrical enclosures, we cut down the motorcycle’s weight. This is crucial for electric vehicles (EVs) because lighter bikes can go farther and perform better.
- Simplified Construction: The monocoque design makes building the motorcycle easier. With fewer parts to put together, production becomes quicker and cheaper. This also makes maintenance simpler, as there are fewer components to deal with.
- Sealed Enclosure: Damon’s HyperDrive creates a sealed, watertight space for the high-voltage battery and electronics. This protects them from the environment and boosts safety by reducing the chance of electrical problems.
- Incorporation of Liquid Cooling: Managing heat is important for EV components. HyperDrive uses liquid cooling with cold plates on the battery modules and electronics. This keeps everything at the right temperature, improving efficiency and lifespan.
Why Integrated Design Changes the Game for Electric Motorcycles
HyperDrive’s monocoque structure houses all essential components, removing the need for extra cases and cooling systems. This integrated electric motorcycle design offers several benefits:
- Cost Reduction: Fewer parts and simpler assembly mean lower manufacturing costs. These savings can lower the price for consumers.
- Maximized Battery Capacity: With less space used for redundant parts, more room is available for a larger battery. This directly increases range and performance.
- Optimized Weight Distribution and Aerodynamics: HyperDrive’s shape is designed to fit perfectly with the motorcycle and rider’s aerodynamics. This setup ensures the best rider position and maintains the right center of mass. It improves efficiency for cornering, braking, and accelerating, enhancing traction and stability.
How Damon’s Hyperdrive Redefines Manufacturing and Scalability
HyperDrive is designed for large-scale production. This means it uses high-volume manufacturing methods to balance cost, quality, and performance. One key technique is large die casting. This process molds the case with built-in features like mounting points for the subframe, motor, rear suspension, and radiator.
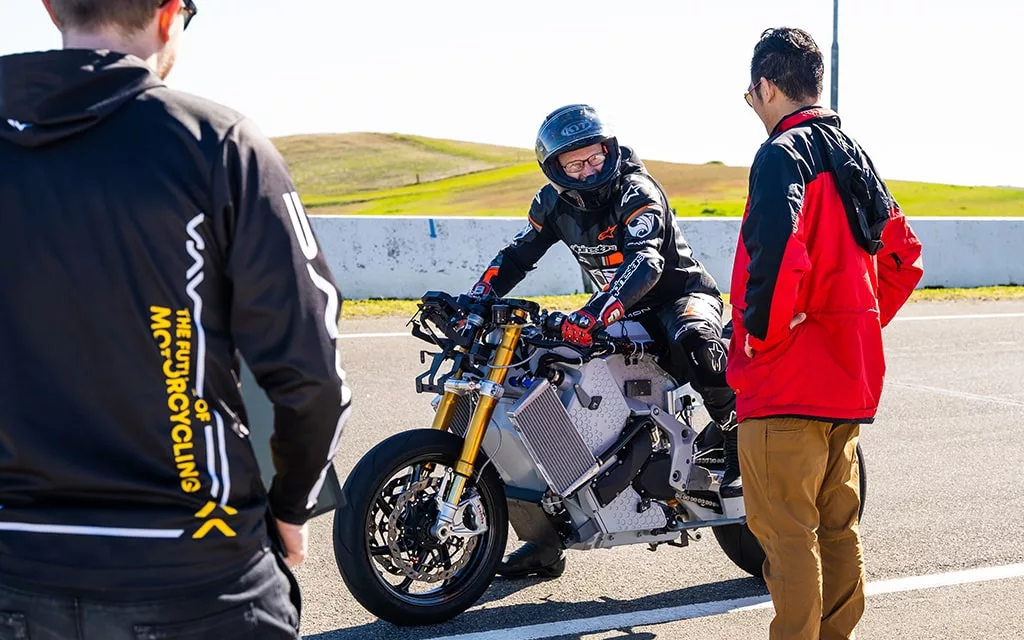
This method is part of a trend called “up integration,” where a single large casting replaces many smaller parts. This approach cuts costs, simplifies manufacturing, and often results in a lighter and better-performing product. A well-known example is Tesla’s megacastings, which use large cast parts to build electric cars. The main challenge is finding or creating machinery big enough for these castings.
Here’s how HyperDrive achieves this:
- High-Pressure Die Casting: Creates the case with precision and strength for mass production.
- CNC Machining: Fine-tunes the die-cast aluminum case for high-performance components.
- Injection Molding: Produces internal parts like battery frames, ensuring consistent quality.
- Stamping: Adds to production efficiency and scalability for various components.
By investing in these methods, Damon lowers costs and improves quality, making high-performance electric motorcycles more affordable.
Simplified Serviceability: How HyperDrive Makes Maintenance a Breeze
In addition to its innovative design and manufacturing, HyperDrive is engineered for simplified serviceability, making maintenance easy and cost-effective. Serviceability is crucial in HyperDrive’s design. Power electronics and the charge port are in sub-assemblies that are easy to access through sealed covers. This makes maintenance and repairs simple, reducing downtime and costs for owners.
How The Motorcycle Chassis Has Evolved
To fully appreciate the innovation behind HyperDrive, it’s helpful to understand how motorcycle chassis design has evolved over the years.
In the 1930s and 40s, motorcycle chassis were made with a single steel backbone. This design was simple but effective.
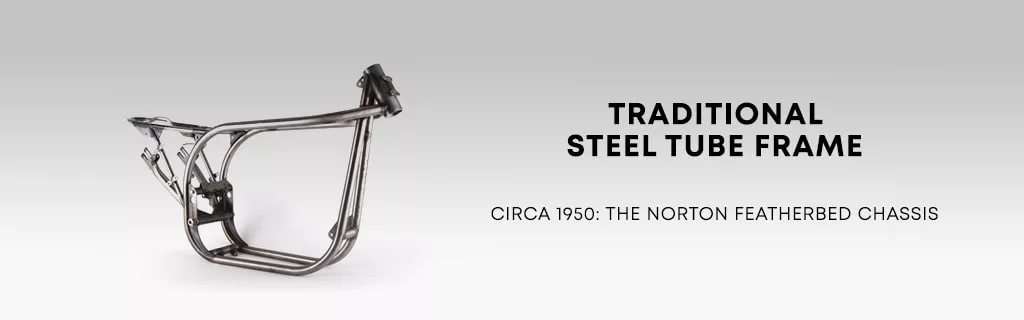
A key innovation came when McCandless developed the cradle type frame for Norton. This design moved the frame tubes outward, making the structure stiffer.
Today’s motorcycles often use a modern “twin spar” aluminum chassis. This design builds on the cradle frame, using lighter materials to achieve similar strength.
The monocoque chassis takes this further. The term “monocoque” comes from French, meaning “single shell.” This design integrates the body and frame into one piece. It started in the aviation industry to make lightweight and strong airframes. Over time, it moved to cars and motorcycles, where it reduced weight and increased strength.
Motorcycle frames have changed a lot over the years. They started with steel tubes, but as performance demands grew, manufacturers switched to complex aluminum designs. A big step forward was the aluminum perimeter frame. This frame, used in bikes like the Ducati Panigale, provides superior rigidity and handling. The Ducati Panigale’s design even uses the engine as part of the structure, making the bike lighter and stiffer.
Earlier, the JPS Norton racer was one of the first to use a monocoque chassis in motorcycles. This showed how well this technology could work in high-performance bikes.
The Future of Motorcycles: What’s Next for Damon’s HyperDrive?
HyperDrive is more than just an innovation; it’s a platform for future motorcycles by Damon Motors.
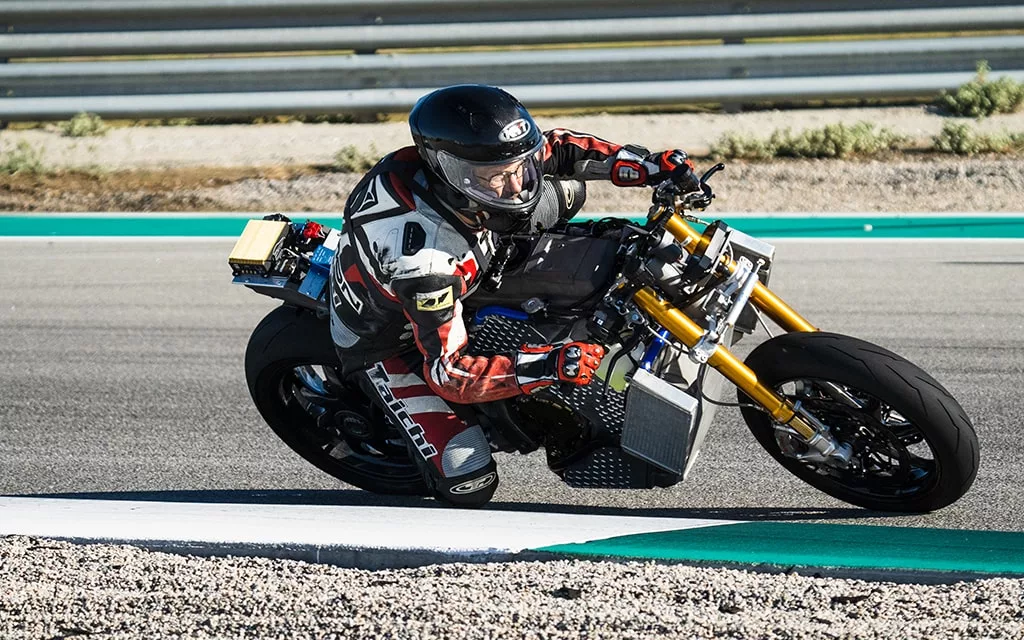
As technology advances, HyperDrive will support new models, allowing each to benefit from ongoing improvements in design and manufacturing.
Conclusion: How Damon’s HyperDrive Sets a New Standard in Electric Motorcycles
Damon’s HyperDrive showcases the innovative spirit at Damon Motors. By using a monocoque chassis, we’ve created a lighter, more efficient, and easier-to-produce electric motorcycle. This design meets modern riders’ needs and sets a new standard for electric motorcycles. We are excited to continue pushing the boundaries of what’s possible and look forward to sharing more updates with enthusiasts and the technical community. Thank you for joining us on this exciting journey.
Related Posts
Search
Categories
Recent Posts
- How Damon’s HyperDrive is Changing Everything we know about Motorcycle Design
- 9 Things To Avoid When Buying Your First Motorcycle
- Do You Need a License for an Electric Motorcycle? (And Other FAQS)
- The Complete Guide to Electric Motorcycle Incentives and Grants [USA Edition]
- The 8 Must-Have Gadgets for Motorcycle Riders